PFD iOI Announces Updates On The RAD/iKnee Lab Installation
PFD MANAGEMENT
OPPORTUNITY FUND 3001, LLC
23161 Lake Center Drive, Suite 100
Lake Forest, CA 92630
Telephone (661) 665-6074, Toll free (888) 475-4748
FOR IMMEDIATE RELEASE
DATELINE: February 10, 2023 Lake Forest California
Announced today by Robert Pryke PFD Capital Partners, LLC, Director and Fund manager for PFD Management Opportunity Fund 3001, LLC, additional points of interest related to its RAD/iKnee portfolio project.
UPDATE OF THE 3D PRINTER IN THE PFD/iOI RAD/IKNEE LAB
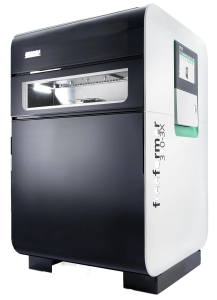
ARBURG Freeformer 300-3X
As discussed in the prior report, PFD/iOI had purchased and was waiting for delivery of a custom Polymer Quadrathane™ 3D printer from ARBURG. As of this date, PFD/iOI is proud to announce the installation of the ARBURG Freeformer 300-3X printer has been completed and the company is now in the process of running its initial test mold prototype printing of the RAD/iKnee device in order to establish its production and manufacture protocols in advance of its ISO 13485 certification.
The ARBURG Freeformer 300-3X is an industrial quality free-form injection molding system
that is capable of taking up to three qualified granulate materials and using a proprietary jetting method that heat melts and discharges the materials with a high level of precision to fabricate thermoplastic parts. The large 23 x 13 x 20 build chamber allows the printer to build complex structured parts and its unique three-port injection system allows a separate support material to be simultaneously printed where the material thickness or the vertical angle of the printed part might be compromised without an underlying material to maintain the integrity of the finished product shape design.
Arburg GmbH + Co KG (ARBURG) is one of the world’s leading manufacturers of high-end injection molding machines for plastics processing. Founded in 1923 and located in Lossburg, Germany. The company operates out of 33 locations in 25
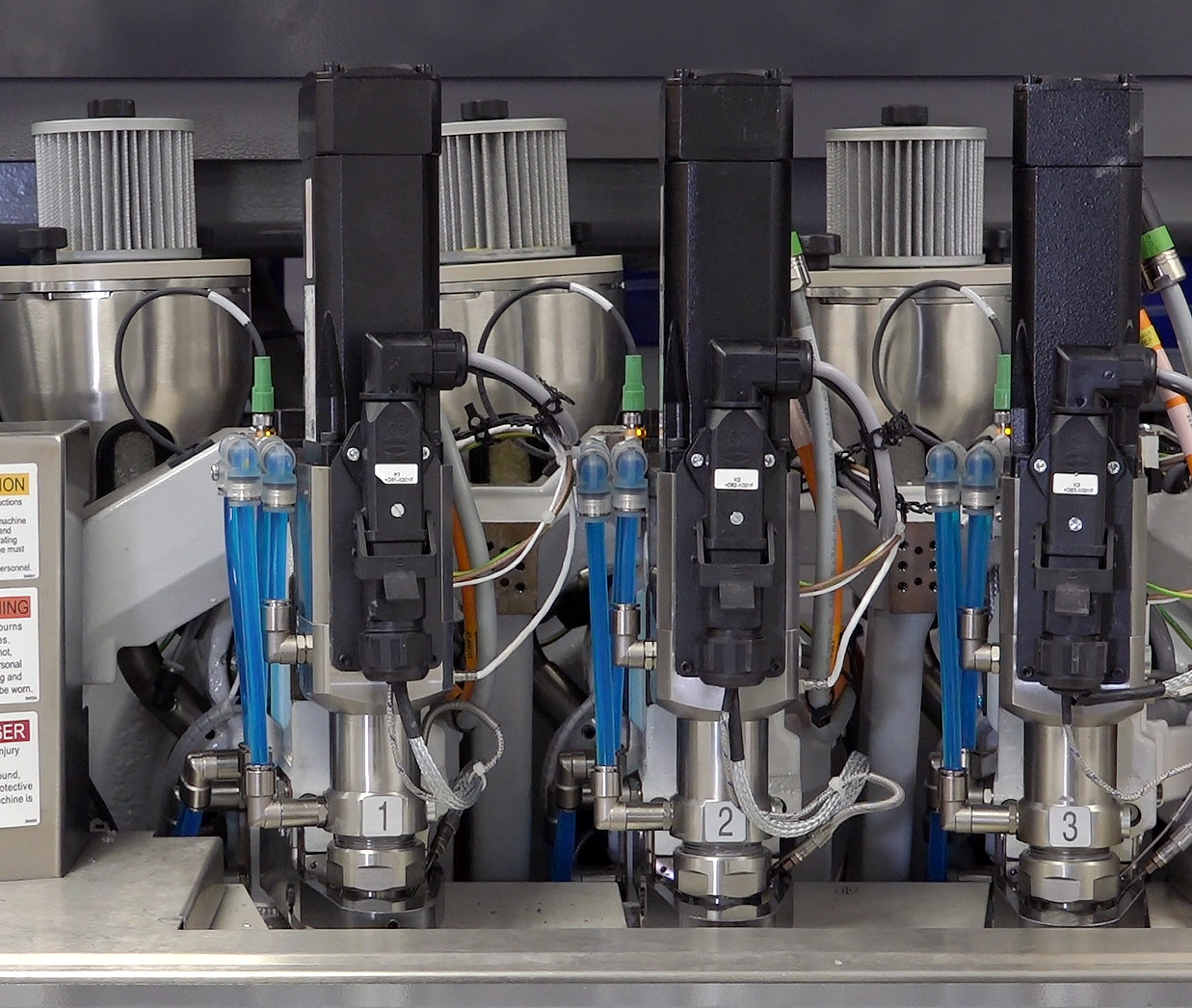
Arburg provides simultaneous injection of three separate materials
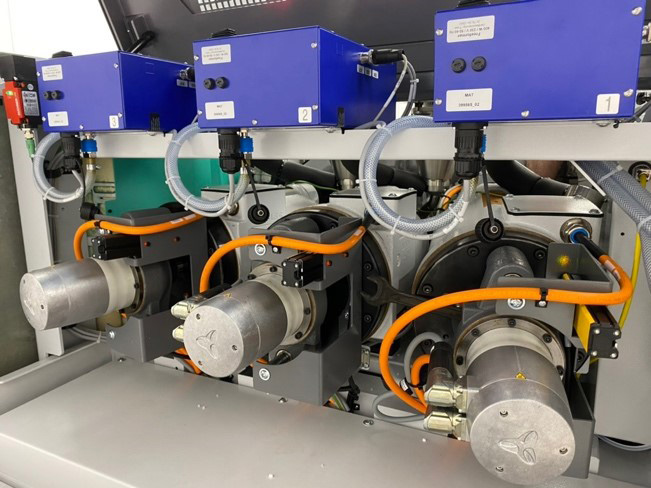
Injection is individually controlled by three separate motors.
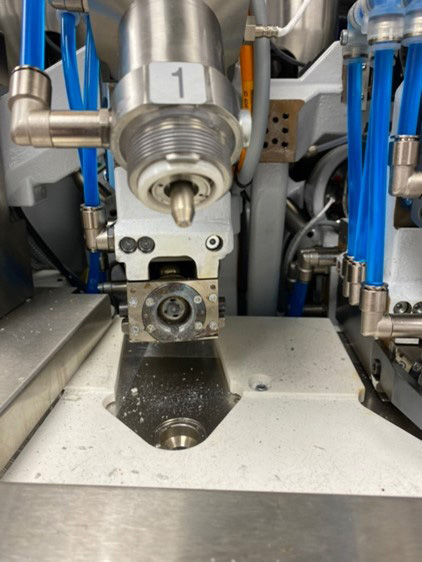
Print nozzles provide precision controlled material injection.
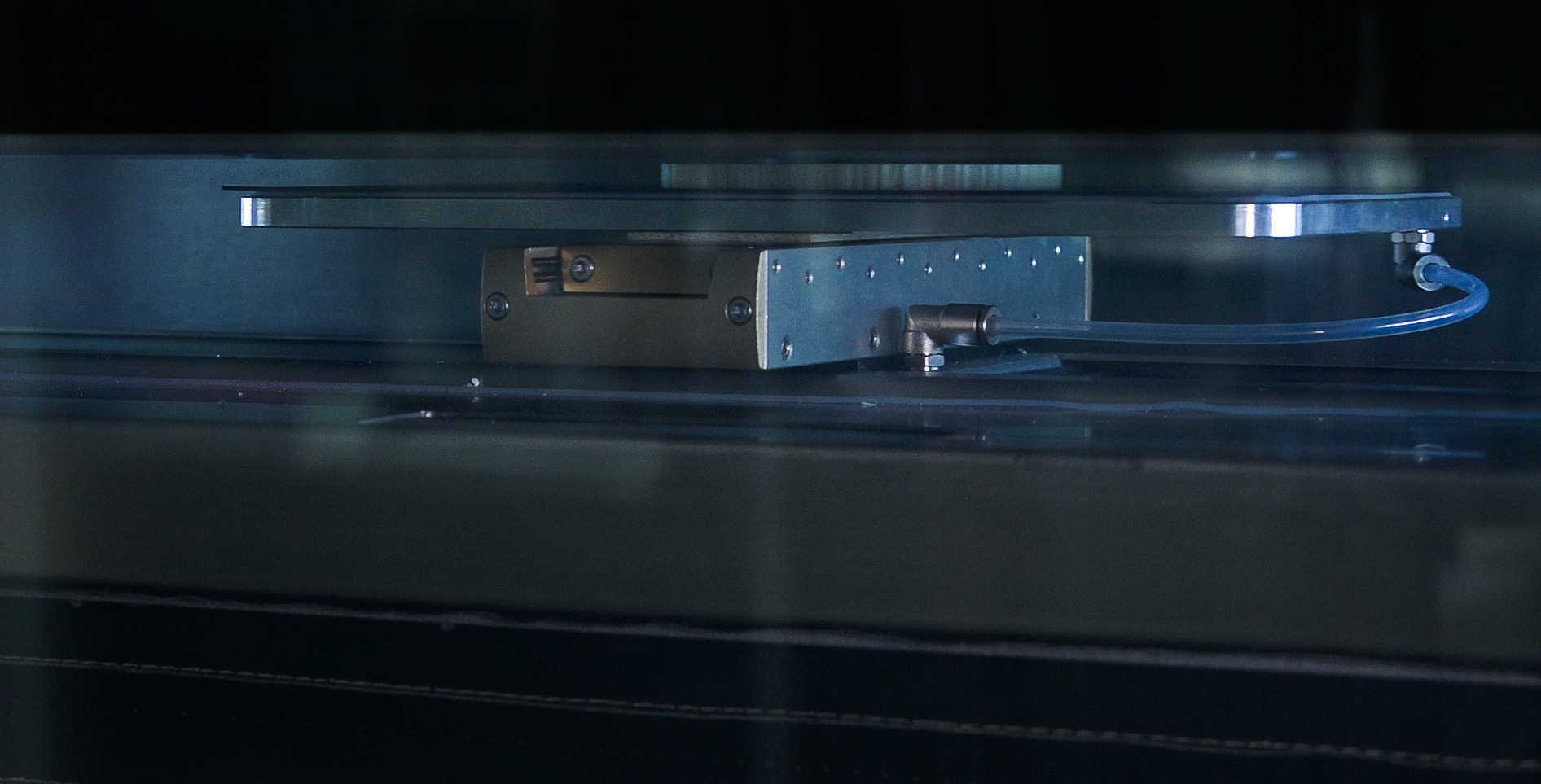
Computer controlled print head delivers consistent repeatable builds.
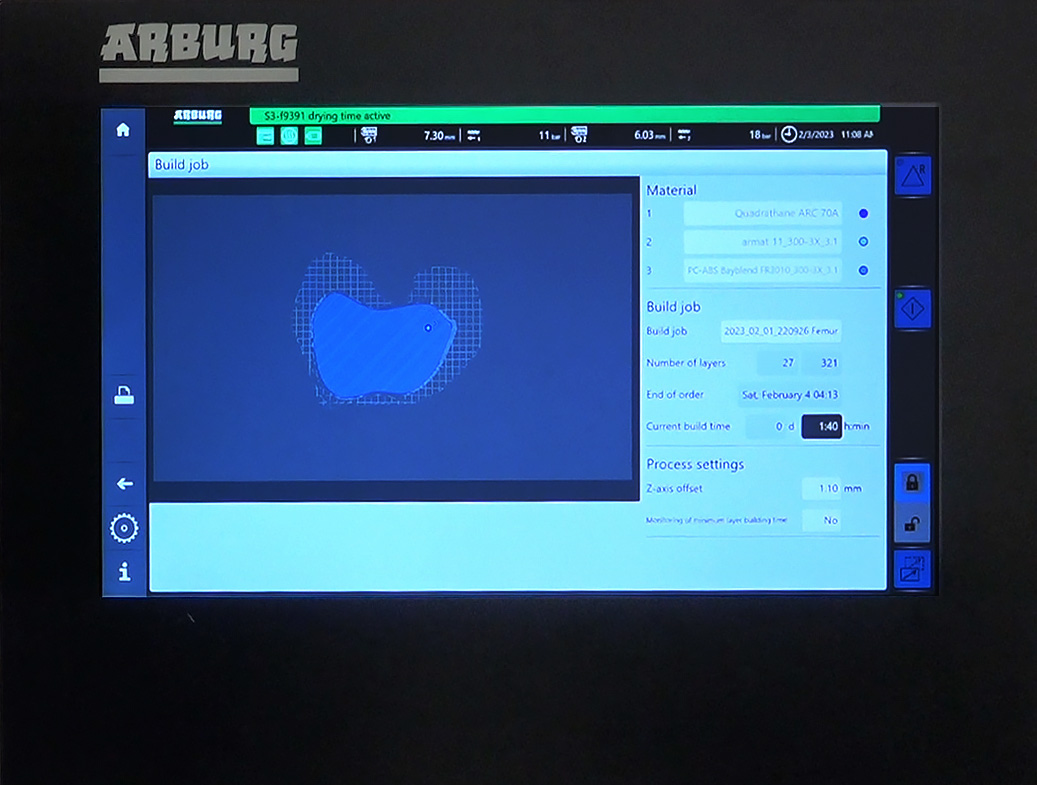
System monitor provides real-time build information and machine control.
countries employing more than 3,000 workers along with trading partners in more than 50 countries. The company generates more than $80M in revenue per year.
As it pertains to the PFD/iOI venture, the ARBURG Freeformer 300-3X is the only printer in the world that is capable of creating medical-grade thermoplastic parts using the Quadrathane polymer which is the material used to construct our RAD/iKnee device. Quadrathane is a polyurethane-based thermoplastic that offers superior bio-compatibility, superior chemical resistance, and oxidative stability for use in long-term body implantable applications. Quadrathane is used across a wide range of medical applications including chronic indwelling catheters, feeding catheters, pacemaker leads, coatings, orthopedics, and other applications where superior chemical resistance is required. For the iKnee, PFD/iOI is using the ARC 70 A Quadrathane which is a naturally clear material that is both USP Class VI and ISO-10993 compliant. The hemocompatibility of the material is perfect for the iKnee in that it provides for safe long-term integration of the iKnee implant into the blood-rich environment of the knee joint with minimal risk of adverse reaction.
The ARBURG Freeformer 300-3X was installed at the PFD/iOI RAD/iKnee Lab located in Los Angeles, CA. The lab occupies a 400sq/ft space in a Class 10 designated clean room facility to allow for the required sterile environment needed for the bio-compatible production of the iKnee. The room provides advanced HEPA filtration that assures no particles greater than five microns, less than ten particles/cubic ft. greater than 0.5 um, and less than 30 particles/cubic ft. greater than 0.3 microns. The room also provides more than 300 changes of the air volume in the room to be made per hour.
The specific requirements for the Class 10, or ISO-4 are:
-
- Up to 1,200 0.3-μm sized particles per square meter
- Average airflow velocity of 0.254 – 0.457 meters/second (or 50 – 90 ft/min)
- Air changes per hour: 300 – 540
- Fan/filter unit (FFU) coverage of 50 – 90%
- ULPA Filters required
- Test particle count every 6 months; airflow and air-pressure differential every 12 months
The PFD/iOI RAD/iKnee Lab is located in Inglewood, CA by the LAX International Airport. This building houses several companies including an aerospace component manufacturer that supplies strategic component parts and systems for the Department of Defense and an advanced medical technology company. The facility includes one of the few privately funded and FDA-certified animal testing surgery centers in California.
This facility has a long track record of providing R&D support for several proven advanced medical technologies including:
-
- Catheter Guidance Control and Imaging (CGCI) System – an intelligent guidance platform developed by Magnetecs Corp. for the magnetic navigation of catheters inside the highly dynamic environments of the human body.
- Optikus Pathogen Detection System – a portable handheld device that provides rapid pathogen detection of a fluid sample based on a biomarker of interest. This technology developed by Sensor-Kinesis Corp. was acquired by TACO Ventures headed by Larry Ellison for commercial development.
- The Huygens™ Catheter and the Proteus™ Robotic Arm – an advanced EP mapping catheter capable of providing accurate detection of electrical signals in the low microvolt range to provide a heart map that is more than 200x greater in resolution than current mapping technologies. The system being developed by Neuro-Kinesis Corp. is one of the medical technology companies in the PFDMOF3001 Opportunity Fund being offered by PFD Capital Partners.
With the installation and setup now complete, PFD/iOI is now working on refining its production technique for the iKnee and has already produced several test models. At the same time, PFD/iOI is finalizing its Quality Management Systems (QMS) documentation as well as establishing its QMS processes and controls as it prepares to move to ISO 13485 Certification in advance of its initial human clinical trials.
BUILDING ON SUCCESS
The PFD/iOI RAD/iKnee Lab is being operated out of a facility that has, and continues to build on a long legacy of proven IP development and commercialization success. PFD/iOI is very proud to be part of that story.
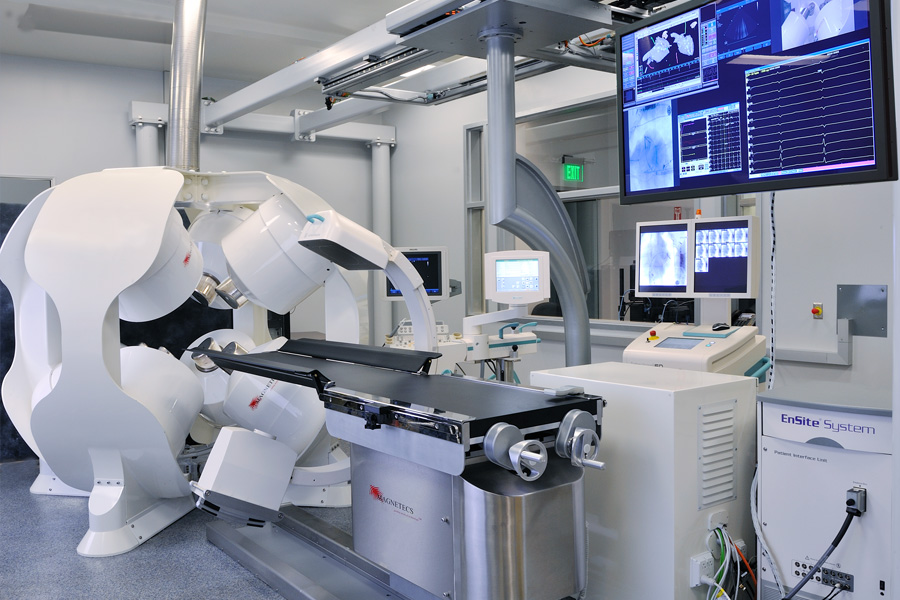
CGCI™
First Robotic-assisted magnetic control system for EP catheter guidance.
97 Patents, CE Mark Certified
Five global installations
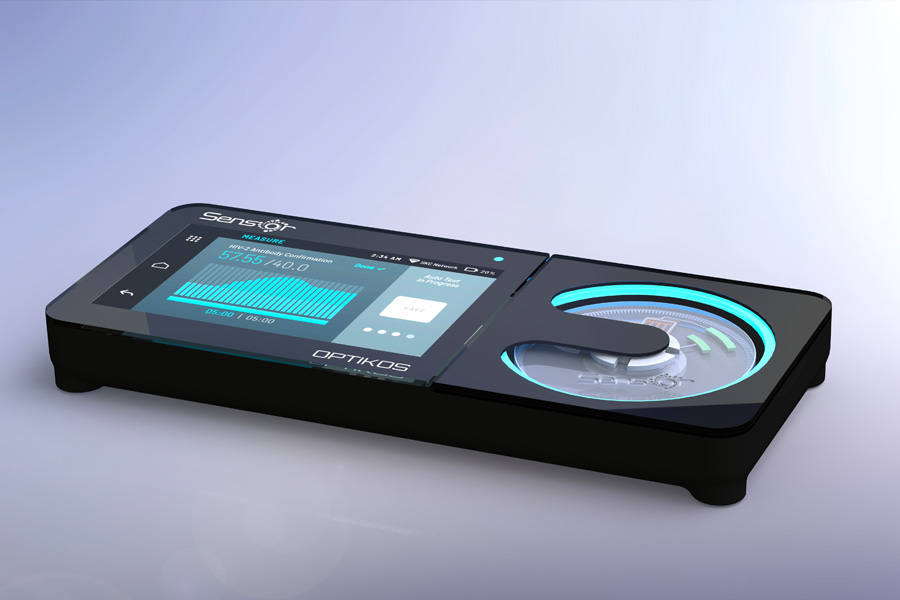
OPTIKUS™
First portable pathogen detection system.
33 Patents
Purchased by Larry Ellison for his AMDI venture.

HUYGENS™/PROTEUS™
First EP mapping catheter to detect low microvolt cardio-signals for improved diagnostics.
10 Patents
Currently in validation studies with Sandia National Lab.
ISO-13485 CERTIFICATION
As stated above, PFD/iOI is seeking ISO-13485 Certification for the company’s operations in developing its RAD/iKnee technology. The ISO-13485 certification is granted by the International Organization for Standardization (ISO) which is an independent, non-governmental organization, that helps develop, regulate, and monitor the standards by which manufacturing companies handle their Quality Management System (QMS) processes and Standard Operating Procedures (SOP). In specific, the ISO-13485 is the certification of these standards as it relates to companies in the Medical Device manufacturing category.
The ISO-13495 certifies that a company has created and implemented a comprehensive quality management system for the design and manufacture of a medical device. Though not a requirement for manufacture, the ISO-13485 provides an awarded company market credibility and identity as to its adherence to both industry and governmental safety and best practice standards. The ISO-13485 is also used as the basis for obtaining foreign market certification as the designation is considered to be the in-line standard and requirement for medical devices. The European Committee for Standardization (CAN) uses the Quality Management Systems (QMS) standards defined in the ISO-13485 as a preferred method to prove compliance for medical device manufacturers seeking CE Certification. The ISO-13485 meets the Global Harmonization Task Force Guidelines (GHTF) guidelines which have become the universal standard for the design, manufacture, export, and sales of various medical devices which have also been also adopted by the newer International Medical Device Regulators Forum (IMDRF) protocols.
To achieve ISO-13485, a company must apply for the certification and then undergo a Stage 1 Pre-Certification Audit to evaluate the systems and procedures they have put in place in order to determine if there are any adjustments that need to be made. Once completed, and the company has made any required changes, a final Stage 2 Audit is performed after which the certificate can be granted.
To prepare for this audit, PFD/iOI has begun the development of its needed QMS and SOP documentation which both describes and provides the training and process description for every aspect of the manufacture and testing of its technology platform. These documents are used for everything from parts acquisition and manufacture traceability, to assembly processes and device issue procedures. The QMS and SOP are used both internally for the company’s testing and manufacturing team as well as by its strategic suppliers and Contract Manufacturing Organizations (CMO). Adoption of the SOPs ensures:
-
- the safety, health, environmental, and operational processes and procedures necessary to perform a job properly are in place.
- that all production operations are performed consistently to maintain quality control of processes and products.
- scheduling and production timelines can continue uninterrupted and are completed on a prescribed schedule.
- that a streamlined process for handling process or production failures issues is in place to mitigate risk and downtime concerns.
- that comprehensive and compliant documentation is in place that shows adherence to all company and government regulations.
- training documentation about the process for which the SOP was written, is consistent and minimizes employee or strategic CMO error.
- that a Quality Assurance program checklist is in place for proper performance and manufacture.
- that a documented protocol is in place for auditors for financial, or regulatory compliance issues.
- a comprehensive historical record of the how, why, and when of each step of the manufacturing, testing, and engineering phase of a product is recorded.
PFD/iOI is anticipating it will be ready for its initial Stage 1 Pre-Certification Audit by the end of March 2023.
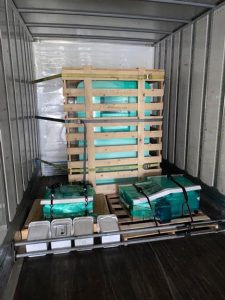
The Arburg arrives at the PFD/iOI lab.
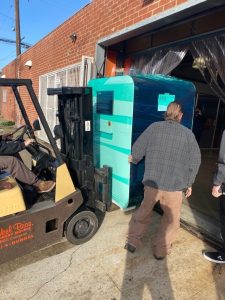
The Arburg being moved into the clean-room.
BUILDING THE LAB
The PFD/iOI RAD/iKnee Lab represents a major milestone in the company’s progress. The Class 10 clean-room facility with the Arburg printer and the peripheral support equipment and workstations allows the company to rapidly work on refining its technology manufacture process in preparation for actual customized patient implants for the upcoming multi-site Comfort Study.
This Is How We Roll!
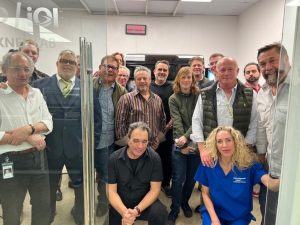
The PFD family poses for a group shot as they prepare for a trial run of the Arburg.
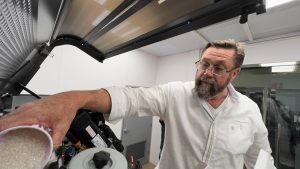
Eric Hansen, PFD Co-founder and Patient One, loads the Quadrathane into the Arburg.
The PFD/iOI RAD/iKnee Lab is up and running and ready for the first test of the Arburg.
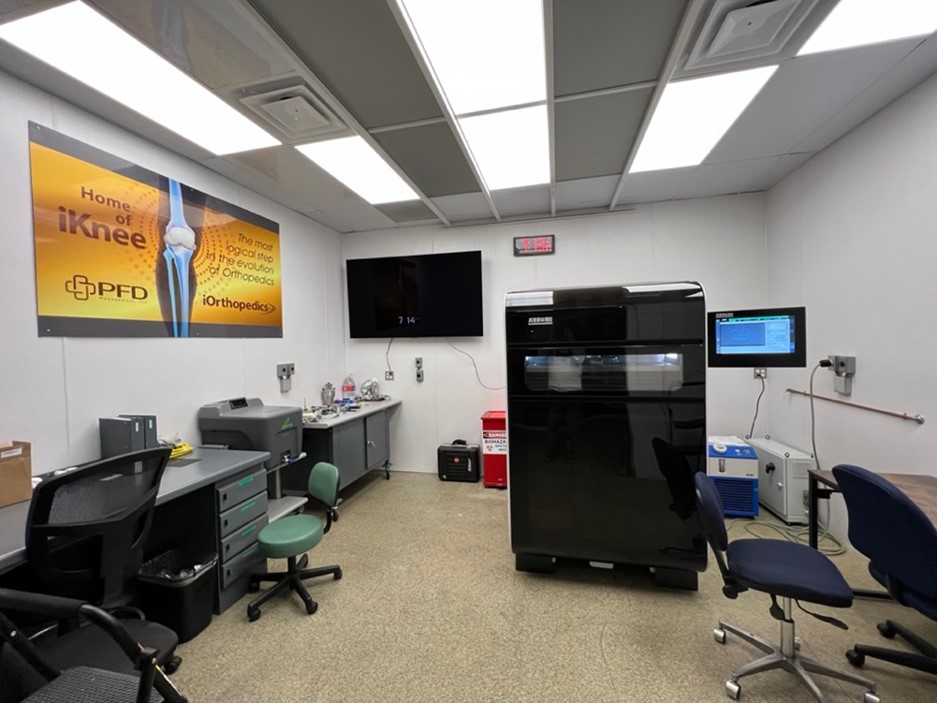
The first iKnee with the support material removed is shown along with the first mold of its complimentary distal femur
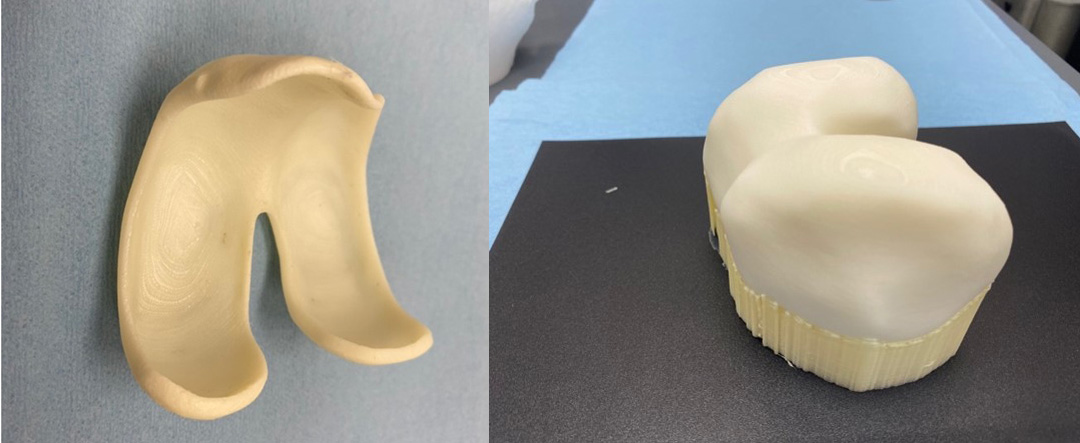
The very first PFD/iOI printed iKnee with the support material rolls out picture perfect.
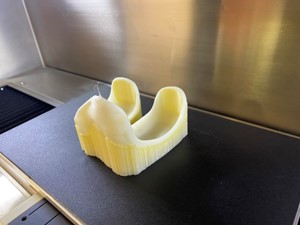
The PFD/iOI RAD/iKnee Lab is now completely operational. During the next several months the PFD/iOI engineering team will be working to establish their manufacturing protocols as it applies to establishing the QMS and SOC requirements for obtaining their ISO-13485 Certification. It is anticipated that the company will be ready for its preliminary audit for the ISO by the end of March, 2023.
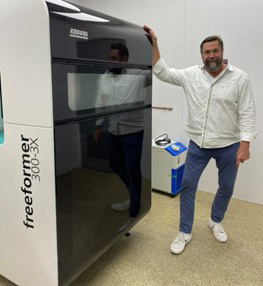
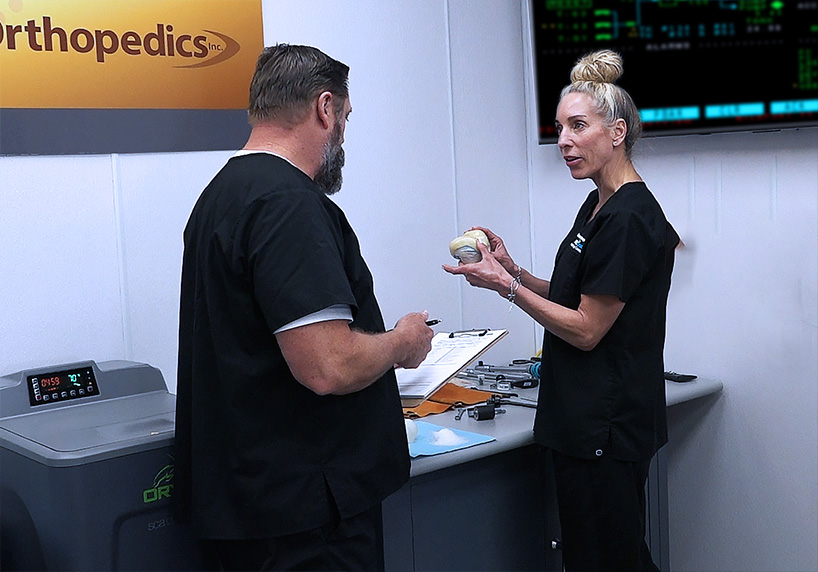
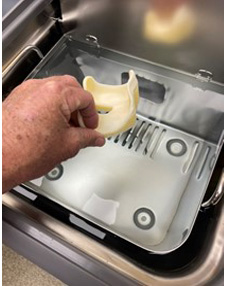
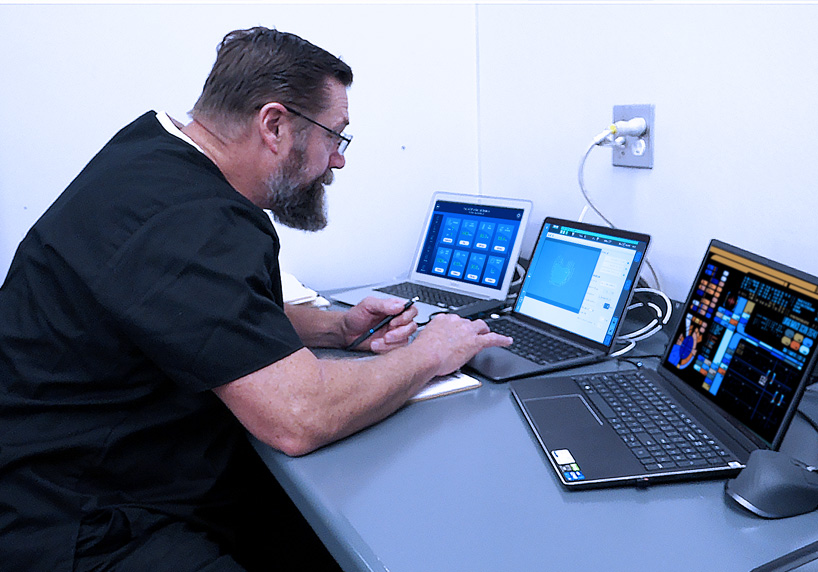
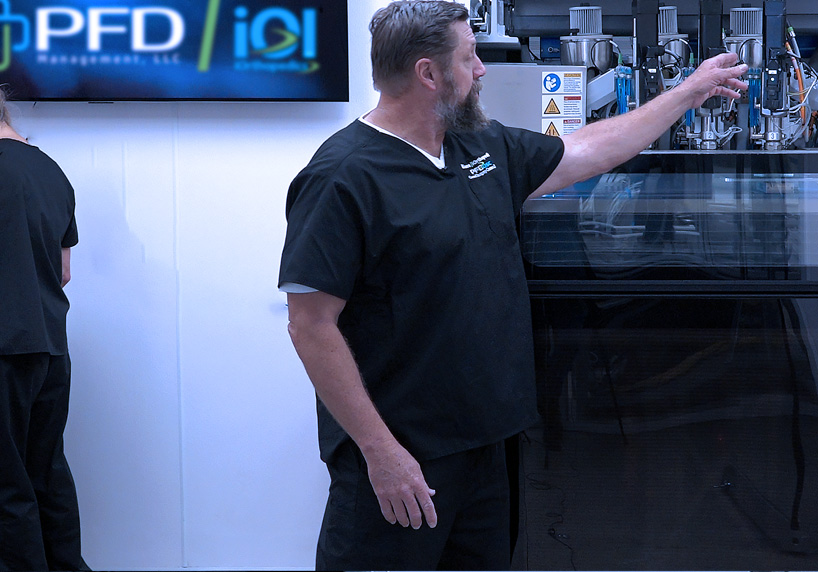
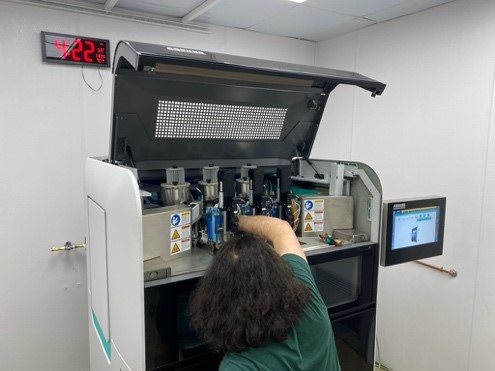
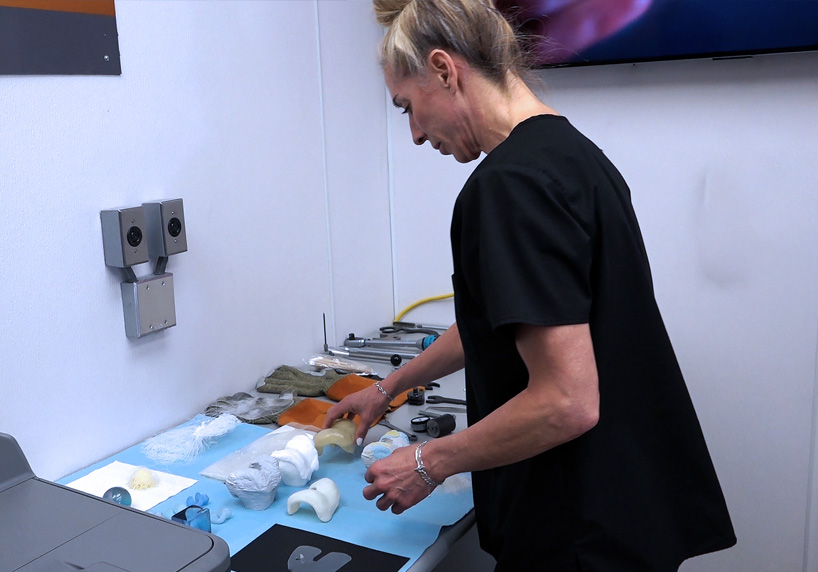
IRB EXTENSION GRANTED
PFD/iOI has been granted an extension of its Investigational Review Board (IRB) protocol document as it prepares for the First-In-Human Proof-of-Concept (FIH POC) trial of its RAD/iKnee technology. As has been stated earlier, PFD/iOI has been granted authorization to conduct up to a 10,000 patient Comfort Study to gather the longitudinal data required to move the iKnee application of the RAD technology to FDA approval and commercialization. PFD/iOI holds an Investigational Device Exemption (IDE) from the FDA that permits PFD/iOI to conduct clinical studies to gather data on the technology’s efficacy and safety based on its qualification of being a Non-Significant Risk (NSR) device.
PFD/iOI has been in negotiations with Advarra Inc. to be the sponsor and manager of its IRB for the iKnee Comfort Study. Advarra is a global leader in supplying IRB, institutional bio-safety committee, and research compliance services to clinical trial sponsors, CROs, hospital systems, academic medical centers, and investigators. On February 7, 2023, Advarra announced that it had completed its review of the submitted protocols for the iKnee Comfort Study and that it agreed to be the IRB sponsor and oversight manager for the study. The approval covers a one-year time period from 02/07/23 to 02/07/24 during which PFD/iOI is planning to commence and completes its initial phase of the trial.
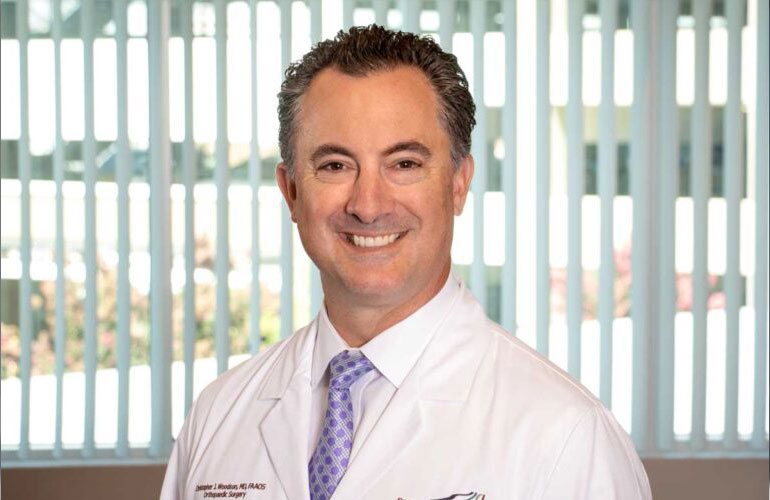
Dr. Christopher Woodson
Principle Investigator
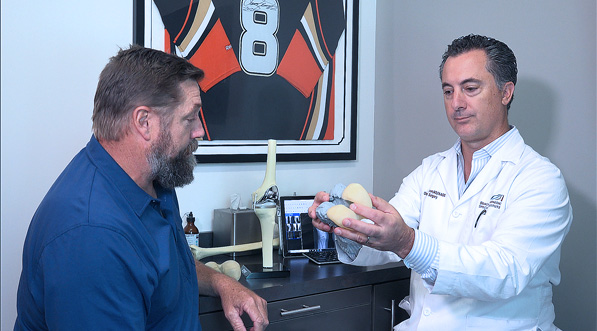
Dr. Woodson reviews procedure for the First-In-Human Proof-Of-Concept implant with Eric Hansen, Patient One in the Comfort study to be performed at the Memorial Care Outpatient Surgical Center in Long Beach, CA.
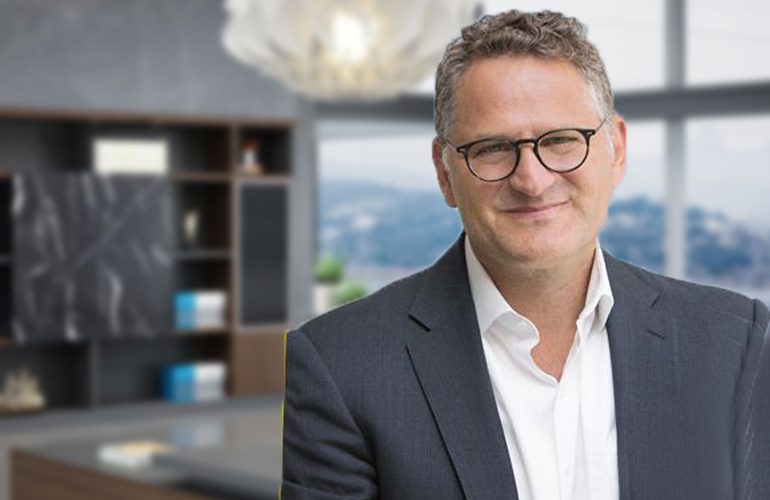
Gadi Saarony
CEO Advaara
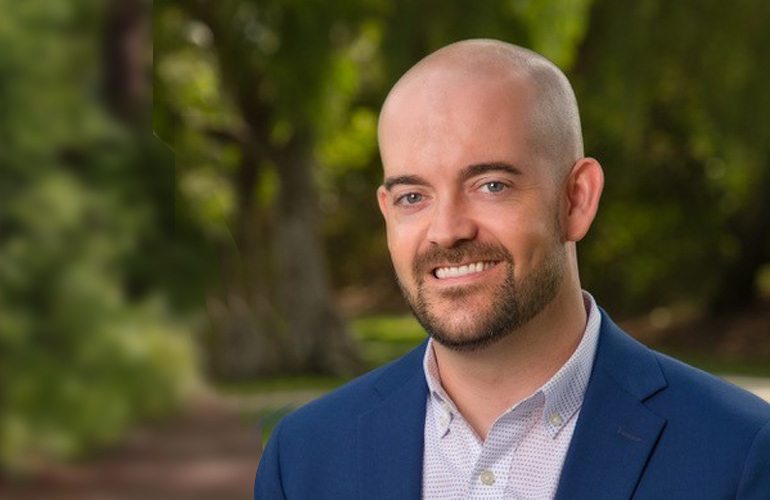
Ryan Helber
Lead Coordinator
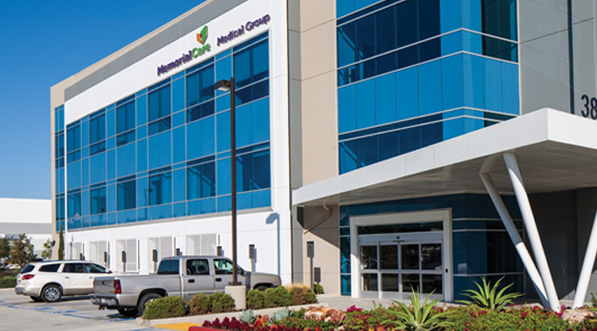
Memorial Care Outpatient Surgical Center in Long Beach, CA.
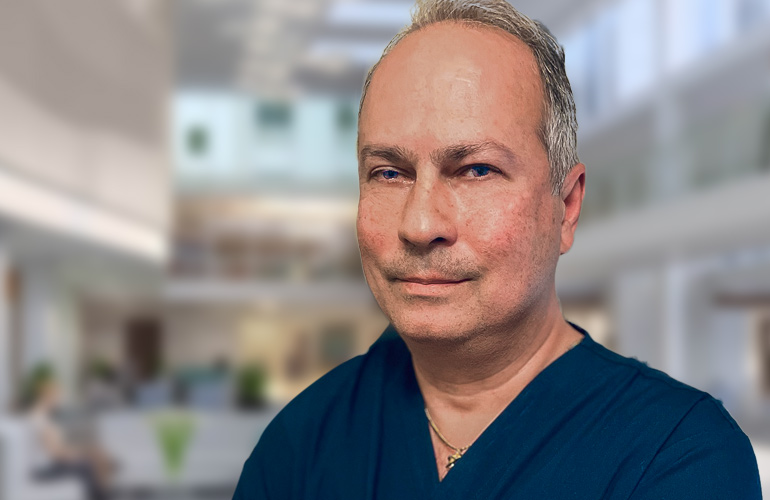
Dr. Daniel Rastein
FDA Liason
PFD has already enrolled its first Comfort Study site as well as Patient One for the FIH POC procedure. The initial implant of the iKnee device will be at the Memorial Care Surgical Center in Long Beach, CA. The initial trial patient will be PFD’s Director, Co-Founder, and Clinical/Asc Operations Manager, Eric Hansen. Eric suffered from debilitating knee pain for more than seven years due to injuries sustained from both sports and heavy use issues. He has attempted several methods to alleviate both the pain and the mobility issues, but to date has found no relief. At this point, his only option would be a Total Knee Arthroplasty (TKA). As such Eric meets all the criteria established in the Comfort Study’s IRB protocols as a candidate for the iKnee implant. It is anticipated the surgery will take place in Q2 of this year with the surgery to be performed by iOI’s Chief Investigator, Dr. Christopher Woodson, who is a board-certified orthopedic surgeon and sports medicine physician, and founder of Beach Orthopedic Specialty Institute. Dr. Woodson will also be serving as the Principle Investigator for the IRB’s Comfort Study.
Based on the success of the initial left-knee implant, PFD/iOI plans to begin enrollment of both trial sites and patients for the next phase of the study. PFD/iOI already has several sites interested in participating in the study as well as more than 200 qualified potential candidates who meet the criteria for the procedure.
Take a moment to check out this short video of Eric Hansen showcasing some of the highlights of the new ARBURG FREEFORMER 300-3X Printer at the PFD/iOI RAD/iKnee lab
About PFD/iOrthopedics. Inc.
The PFD/iOrthopedics INC (PFD/iOI), Resilient Arthroplasty Device (RAD), and its first product candidate the iKnee, has been IRB IDE authorized for human use in the first 10,000 qualified patients.
PFD/iOI is introducing a 21st Century, personalized, patient-driven, novel, and highly disruptive restorative, joint salvage outpatient approach.
It is an effective solution to fill the gaping, costly, inefficient, and non-therapeutic void
between pills, shots, bracings, physical therapies, and the limiting of daily activity for patients
suffering from osteoarthritis.
This additional interventional option may potentially eliminate or at least delay the much
more dramatic, life altering and invasive surgical replacement of joints with a simple
outpatient procedure.
The intent was that this principle would be used in all mammalian joints; think animal and human including the knee, hip, shoulder, etc throughout all the long bone interfaces (appendicular skeleton).
The Resilient Arthroplasty Device (RAD), referred to as the iKnee, is a patented implantable medical device by which patients presenting with osteoarthritis will find pain relief through the padding, cushioning, and protection of the damaged joint surfaces.
The iKnee will change the pain profile by covering the dominant surface of the damaged joints very much like the original cartilage.
Strategic Alliances
The following is provided for purposes of giving the reader deeper appreciation of the strategic alliances involved with bringing the PFD/iOI technology to commercialization.
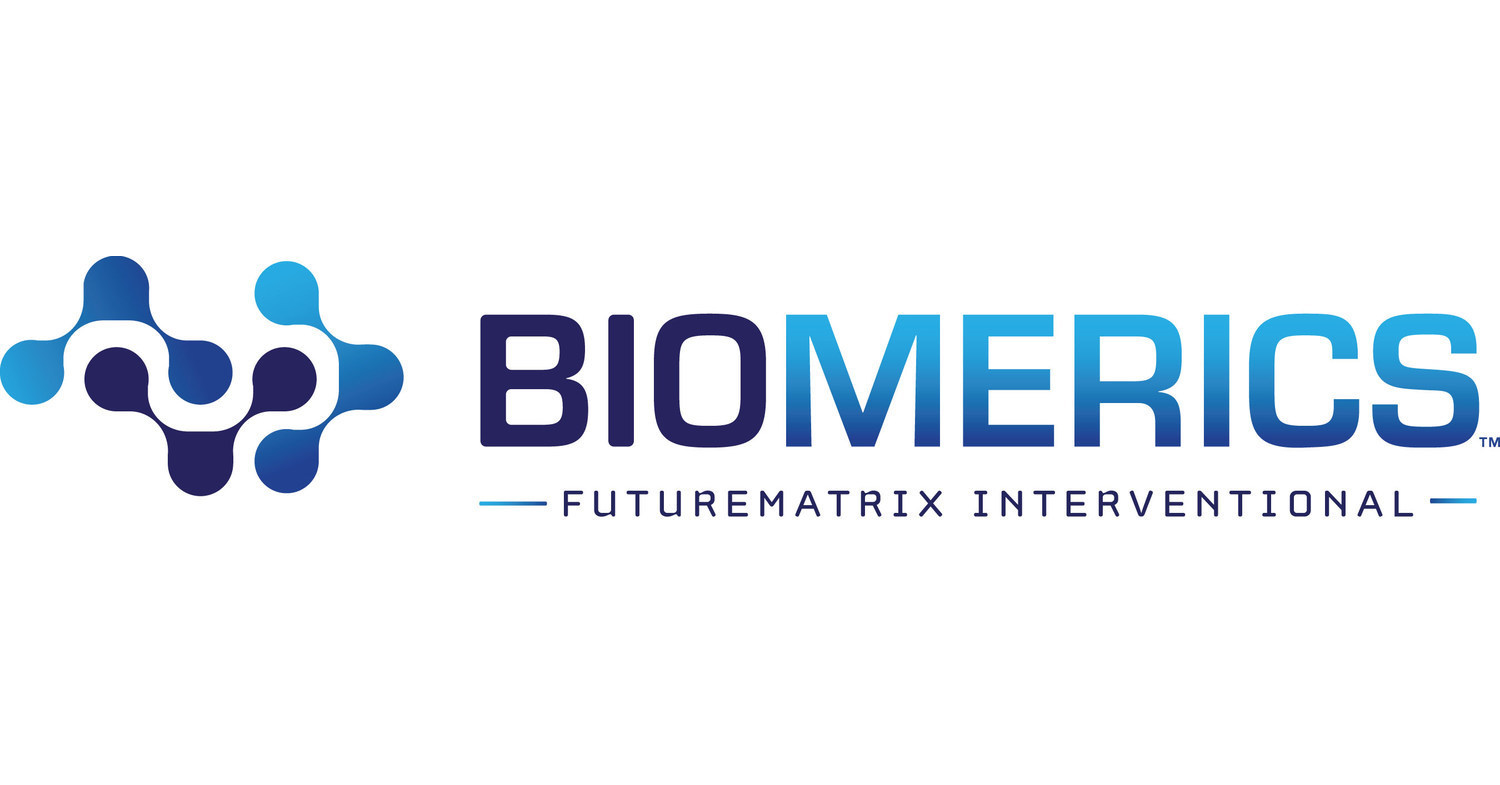
QUADRATHANE
Quadrathane™ ARC is a family of aromatic polycarbonate-based thermoplastic polyurethane. It offers superior biocompatibility, superior chemical resistance, and oxidative stability for use in long-term body implantable applications. It is naturally clear, hemocompatible, and is USP Class VI and ISO-10993 compliant. Quadrathane™ ARC is used across a wide range of medical applications including chronic indwelling catheters, feeding catheters, pacemaker leads, coatings, orthopedics, and other applications where superior chemical resistance is required. The iKnee will use Quadrathane ARC 70 A.
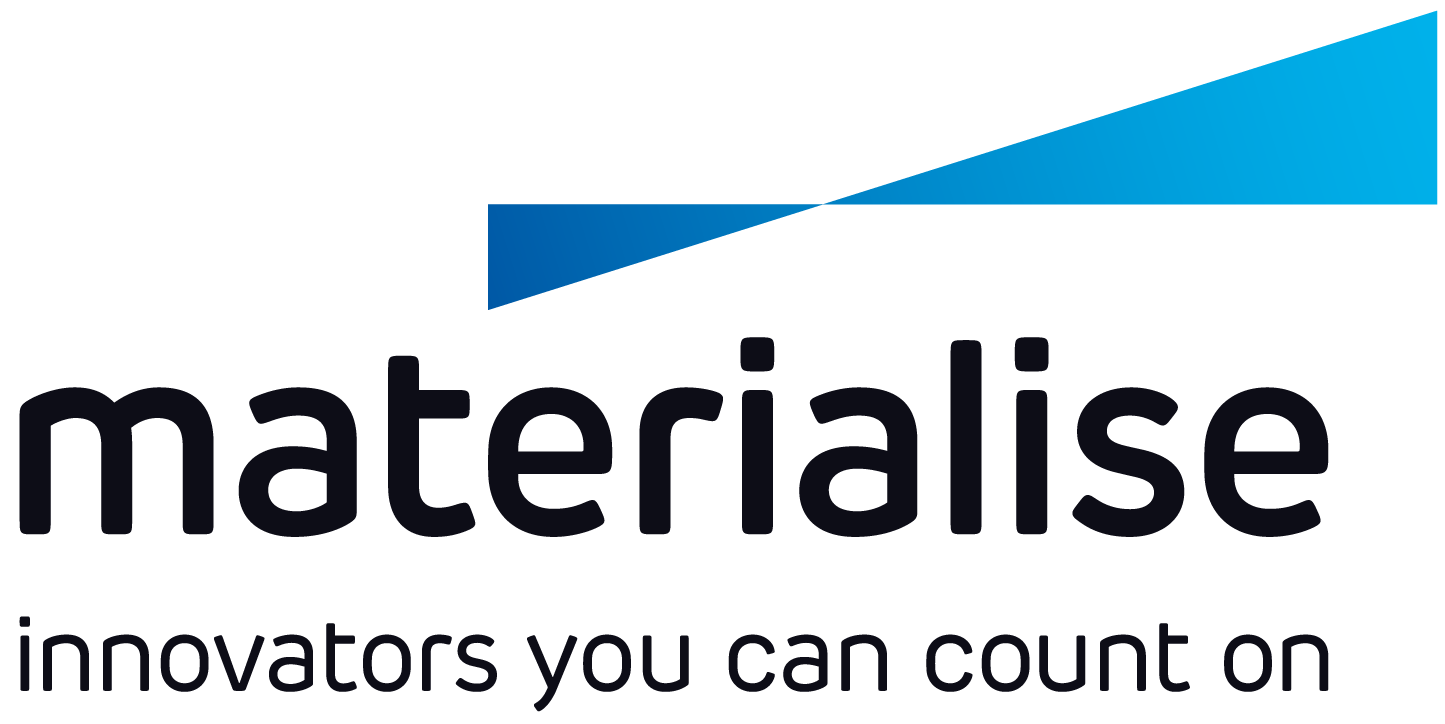
Mimics Innovation Suite
In furtherance to complete comprehensive personalized medicine, PFD/iOI has utilized Materialise, as the industry-standard medical image-based engineering software and service, MIS puts us in control with the most advanced tools to support our mission to improve patient care. Medical image data thus serves as a powerful basis for engineers and researchers striving for solutions that will lead to safer and more predictable personalized patient outcomes.
The Mimics Innovation Suite was designed to make using medical image data for engineering purposes as easy and rewarding as possible.
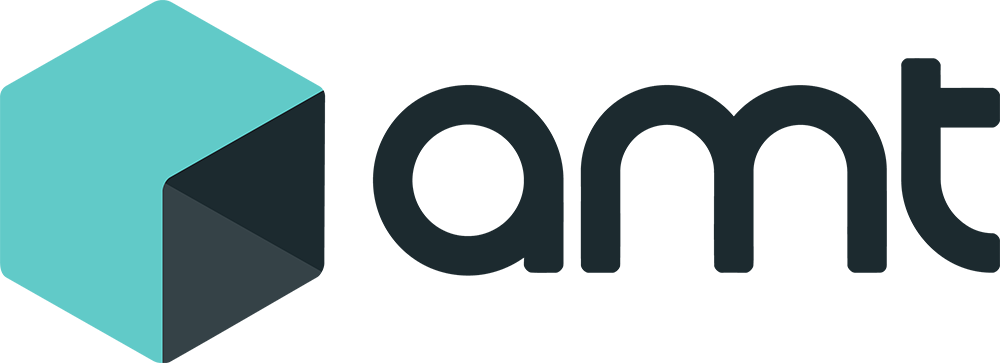
Production of a 3D Printed Part Doesn’t Stop at the Printer.
Post-processing is required to finish 3D-printed parts for end use. Traditional methods are slow, difficult to predict consistency, and can account for up to 60% of the part cost.
PostPro, developed by AMT, is a digital post-production technology platform that automates the manual and costly steps associated with legacy 1.0 ‘low volume and prototyping’ post-processing and enables functional ‘high-volume end-use parts’ production from 3D printers.
PostPro allows companies to leverage the benefits of additive manufacturing at scale, by providing an order-of-magnitude improvement in part throughput, performance, quality, cost, and safety.
The benefits of vapor smoothing to seal surfaces for easier cleaning and sterilization are a game changer for the medical and food industries.
Vapor smoothing surfaces prevents liquid absorption, allowing for the development of new applications in numerous industries. Vapor smoothing the parts in preparation for surface coating and dying will significantly reduce the time needed to get perfect results.
Repeatability and consistency of performance results directly enable the scaling up of manufacturing processes and volumes.
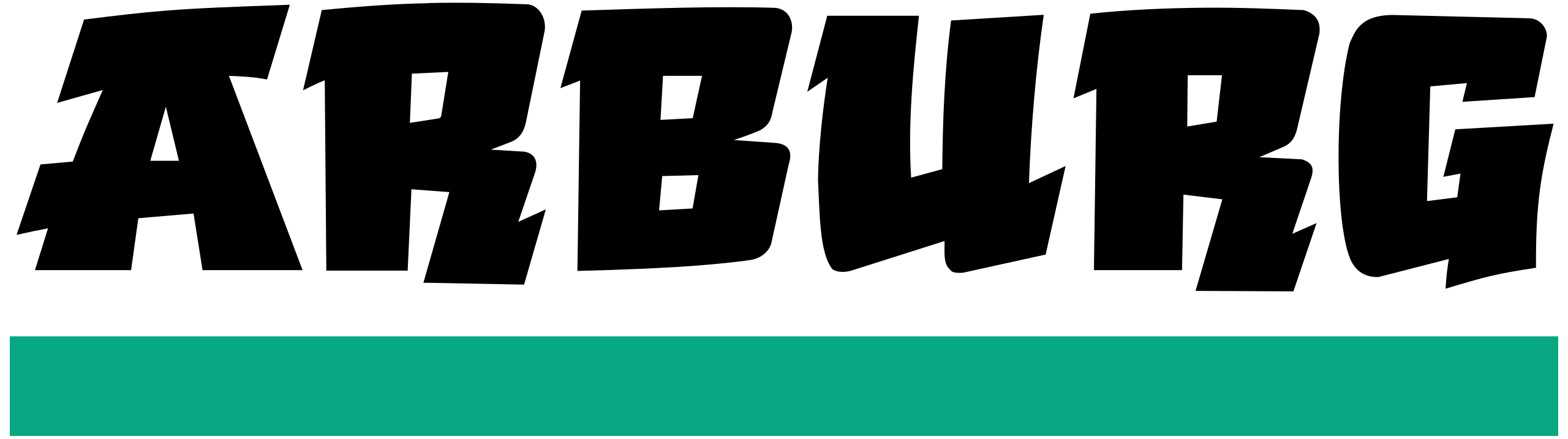
Arburg Plastic Freeforming
ARBURG Plastic Freeforming (APF) technology uses qualified standard granulates employed in injection molding technique. Using the material jetting method, these granulates are melted and discharged to fabricate thermoplastic parts. Freeformer 300-3X is an industrial 3D printer produced by ARBURG additive. ARBURGadditive is a 3D printer manufacturer based in Germany. The Arburg Freeformer 300-3X will be placed in our PFD/iOI RAD printing Clean Room. This room contains 3-phase electrical with compressed air and Oxygen and Nitrogen. The lab consists of three different spaces that allow the company the ability to test prototype designs, perform quality control checks, and establish operational and test protocols while gathering the important analytical and comparative clinical data needed to further its regulatory approval strategy.
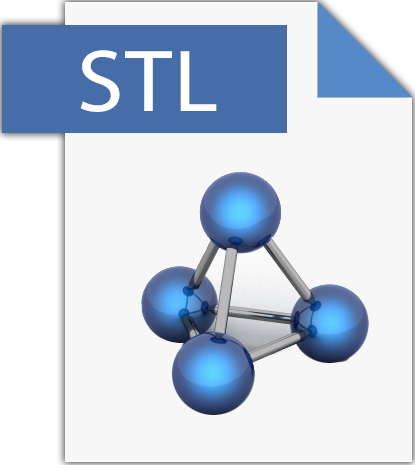
STL File
The STL file format is the most used file format for 3D printing. When used in conjunction with a 3D slicer, it allows a computer to communicate with the 3D printer hardware. The STL file format has been adopted and supported by many CAD software packages. Today it is widely used for rapid prototyping, 3D printing, and computer-aided manufacturing.
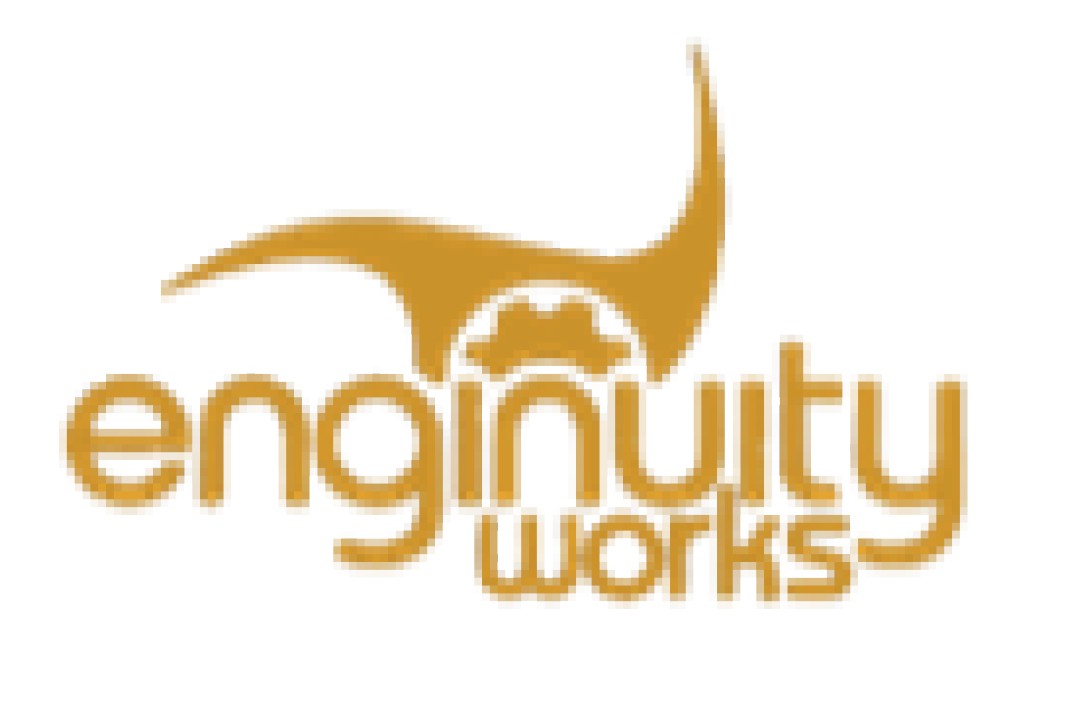
Enginuity Works
Enginuity Works provides our engineering consultation for the full range of product development services, Industrial Design, Mechanical Engineering, Electrical Engineering, Prototyping, R&D, and Manufacturing Management. Their approach identifies the best fit of our own expertise and capabilities with their engineering team.
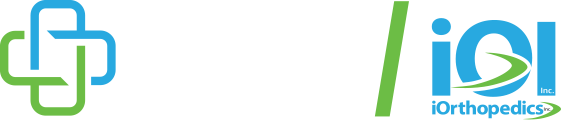
has initiated the protocols for a comprehensive clinical trial to validate the iKnee Resurfacing in order to achieve regulatory certification in order to bring the procedure to first application commercial use.
IKNEE COMFORT STUDY
Description: the iKnee seeks to provide temporary comfort and improved function for patients awaiting total knee replacement arthroplasty (TKA). Reasons to delay a TKA include but are not limited to the need for weight loss, wound infection healing, implant availability, and required medical or psychological patient preparations. iKnee use determinations are made between the patient and caretaker. The subject population is individuals with refractory disabling knee pain who failed other conservative measures and are on track for TKA. The iKnee is to provide comfort, it is not intended to treat a disease, or underlying cause leading to TKA.
Objective: To study iKnee efficacy on quality of life and activities of daily living in patients awaiting TKA. The data will be used to improve possible designs to enhance patient comfort.
Procedure: A rolled polymer is inserted through a small parapatellar incision and then expanded to fit and pad the distal femur, providing a stable cushion made of medical polymers used safely and reliably for decades. The procedure is expected to take about 30 minutes, and involves an incision of 2-3 cm of subcutaneous tissue into the joint capsule, and an incision less than one cm in depth. The iKnee device is then inserted into the knee capsule. No muscles, tendons, or ligaments are cut.
Study Rationale: Total Knee Arthroplasty (TKA) has become one of the leading operations for senior citizens, both in cost and frequency. When a patient has a disabling knee condition limiting mobility and quality of life there is only one medical option, TKA. The TKA operation is a significant procedure, involving the removal of the bottom of the femur, the top of the tibia, and part of the patella to make space for the artificial metal and polyethylene prosthesis.
The study is designed to increase the patient’s quality of life, functionality, and comfort while they await the knee replacement operation (TKA). The iKnee procedure poses almost no medical risk to the patient, either as a procedure or as a risk to the patient’s knee as the decision has already been made to remove the joint.
INVESTIGATIONAL DEVICE EXEMPTION (IDE)
An investigational device exemption (IDE) allows the investigational device to be used in a clinical study to collect safety and effectiveness data. Clinical studies are most often conducted to support a PMA. Only a small percentage of 510(k)s require clinical data to support the application. Investigational use also includes clinical evaluation of certain modifications or new intended uses of legally marketed devices. All clinical evaluations of investigational devices, unless exempt, must have an approved IDE before the study is initiated.
Clinical evaluation of devices that have not been cleared for marketing requires:
an investigational plan approved by an institutional review board (IRB). If the study involves a significant risk device, the IDE must also be approved by FDA;
- informed consent from all patients;
- labeling stating that the device is for investigational use only;
- monitoring of the study and;
- required records and reports.
FIRST IN HUMAN (FIH)
A type of clinical trial in which a new drug, procedure, or treatment is tested in humans for the First time. Also called First-in-human study.
The following section is provided as a very basic tutorial on regulatory path and some of the terms, processes, and programs that new medical technologies must navigate to become commercial in the United States.
NON-SIGNIFICANT RISK
The FDA does not regulate Non-Significant Risk (NSR) devices.
The Sponsor has the responsibility of making a Significant Risk (SR) or NSR determination and may utilize the services of an IRB, though this is not required.
The RAD/iKnee device does not refer to curing any disease. We are implanting this minimally invasive device for a patient’s quality of life issues while they await a full TKA. This may be for comfort, mobility, or many other non-disease-related terms.
What is a Non-significant Risk Device Study?
NSR device studies must follow the abbreviated requirements at 21 CFR 812.2(b).
An IRB’s NSR determination is important because the IRB serves as the FDA’s surrogate for review, approval, and continuing review of the NSR device studies.
An NSR device study may start at the institution as soon as the IRB reviews and approves the study and without prior approval by FDA.
TITLE 21–FOOD AND DRUGS
CHAPTER I–FOOD AND DRUG ADMINISTRATION
DEPARTMENT OF HEALTH AND HUMAN SERVICES
SUBCHAPTER H – MEDICAL DEVICES
PART 812 — INVESTIGATIONAL DEVICE EXEMPTIONS
https://www.accessdata.fda.gov/scripts/cdrh/cfdocs/cfcfr/CFRSearch.cfm?fr=812.2
FDA Pathways
FDA designation of the iKnee as an NSR Device. Pathways for commercialization are to be determined based on the commercialization path of the purchaser of IP.
Seven FDA Pathways to Bring a Medical Device to Market
1.) Premarket Notification 510(k)
The Premarket Notification 510(k) pathway is the most common route taken when launching a medical device. Almost all Class II devices and certain Class I devices will require a 510(k).
The purpose of a 510(k) submission is to provide the FDA with documented evidence showing that a medical device is substantially equivalent in terms of safety and effectiveness to a predicate device.
A predicate device is one that is already legally marketed and shares the same intended use and technological characteristics as the new device. The requirement is to compare the new device with the predicate by summarizing information from the design controls process, such as design features and verification testing.
The FDA typically processes 510(k) applications in 30-90 days. Depending on the robustness of the initial application, there may be a period of back-and-forth discussions, which can delay the process. It is important to plan and provide all appropriate documentation at the time of initial submission.
2.) Premarket Approval (PMA)
Class III devices, and any device that cannot provide substantial equivalence to a Class I or Class II device through the 510(k) process, must use the Premarket Approval (PMA) pathway.
The PMA process is the most involved as scientific evidence, typically in the form of a clinical trial, is needed to prove the safety and effectiveness of the new device. The FDA will either approve or reject the application within 180 days. The different steps of the review process include:
-
-
-
-
-
- FDA staff will determine completeness through an administrative and limited scientific review
- FDA staff will conduct an in-depth scientific, regulatory, and Quality System review
- An advisory committee will review and offer any recommendations.
- Any final deliberations will occur, and the FDA will document and notify the applicant of their final decision.
-
-
-
-
Although the premarket approval process sounds intimidating, it is the right option for a high-risk, Class III device.
3.) De Novo
If the applicant is developing a lower-risk, “novel” device and struggling to find a predicate, the De Novo pathway might be the best option.
The De Novo pathway has been around since 1997 but many people do not know about it since it is not very commonly used. Companies that do not qualify for 510(k) clearance, since they cannot provide substantial equivalence to a device on the market, should learn more about the De Novo pathway.
Since comparison to a predicate is not needed, companies have a “blank canvas” when it comes to labeling and can set a standard that may give them a competitive advantage over others. One of the key things to remember about the De Novo pathway is that the device must present low to moderate risk through a robust risk mitigation strategy.
4.) Humanitarian Device Exemption (HDE)
The Humanitarian Device Exemption (HDE) pathway is for devices that are intended to treat or diagnose conditions or diseases that affect small or rare populations.
This pathway involves a two-step process. The FDA must grant a Humanitarian Use Device (HUD) exemption and the device company must then submit an HDE application to the appropriate review center.
Another important requirement is that there cannot be another comparable device on the market that shares the same intended use. The FDA will consider the following when determining if there are comparable devices on the market:
-
-
-
-
-
- The device’s indications for use and technological characteristics.
- The patient population to be treated or diagnosed with the device.
- Whether the device meets the needs of the identified patient population.
-
-
-
-
Part of the rationale for providing this pathway is there may not be a large enough patient population with clinical data to satisfy regular FDA requirements of safety and efficacy. Since these devices may be very crucial to patients with rare conditions, the FDA put them in place to do a proper review to determine if the device can be sold.
5.) Custom Device Exemption (CDE)
Is the company developing a custom device for a specific patient? If so, the device falls under the Custom Device Exemption (CDE) pathway and must meet a very narrow set of criteria.
The device must be created or modified to comply with the order of an individual physician or dentist, typically in the form of a prescription. Not only must the clinician order the device, but it must also be used in the normal course of the professional practice of that physician or dentist.
The product should be specifically designed to treat a unique pathology or physiological condition that no other device is domestically available to treat. It must be assembled from components or manufactured and finished on a case-by-case basis to accommodate the unique needs of the patient.
The FDA even states that companies are limited to no more than 5 units per year of a particular device type.
CDE devices are exempt from PMA or 510(k) submission process, but the company still needs to comply with the following regulations:
-
-
-
-
-
- Design Controls (21 CFR Part 820)
- Medical Device Reporting (21 CFR Part 803)
- Labeling (21 CFR Part 801)
- Corrections and Removals (21 CFR Part 806)
- Registration and Listing (21 CFR Part 807)
-
-
-
-
6.) Expanded Access Program (EAP)
The Expanded Access Program, often referred to as the compassionate use or emergency use provision, is fairly self-explanatory.
It allows an investigational device to be used, outside of a clinical trial, in situations where a seriously ill patient has few if any alternatives.
Although there are often ethical considerations, it may be appropriate to evaluate this option to get early feasibility data for high-risk devices, especially when suitable animal models are unavailable. Like the HDE, this data could then be used to expand the label in the future.
-
-
-
-
-
- Expanded access may be an appropriate pathway for you to choose when all the following apply:
- Patient has a serious disease or condition, or whose life is immediately threatened by their disease or condition.
- There is no comparable or satisfactory alternative therapy to diagnose, monitor, or treat the disease or condition.
- Patient enrollment in a clinical trial is not possible.
- Potential patient benefit justifies the potential risks of treatment. • Providing the investigational medical product will not interfere with investigational trials that could support a medical product’s development or marketing approval for the treatment indication.
-
-
-
-
7.) Product Development Protocol (PDP)
The Product Development Protocol (PDP) is a subset of the PMA process that allows for another pathway for companies with devices in which the technology is well established in the industry.
This pathway allows the company to come to an early agreement with the FDA about how the safety and effectiveness of the device will be shown. The two parties are essentially creating a contract that describes design and development activities, including the outputs of these activities, and acceptance criteria for these outputs.
The company can follow the plan on its own time and report back to the FDA on the agreed-upon milestones. At the end of the process, the company is considered to have “completed” a PDP, which gives them an “approved” PMA.
A managing sponsor of fundraising efforts for the affiliated companies of the PFD family of companies,
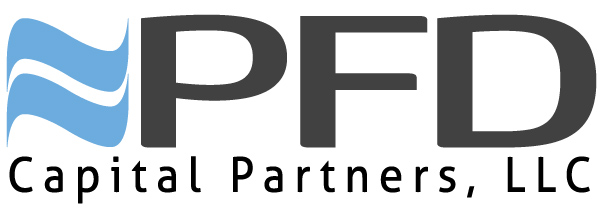
An operational Class A member and manager to the PFD Family Private Equity programs.
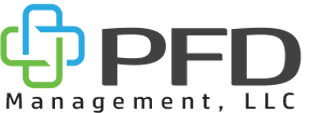
PFD Management, LLC is a vendor to the PFD family of private funds, specializing in sourcing, diligence, underwriting, auditing, packaging, servicing, billing/collecting, and portfolio administration of account receivables.
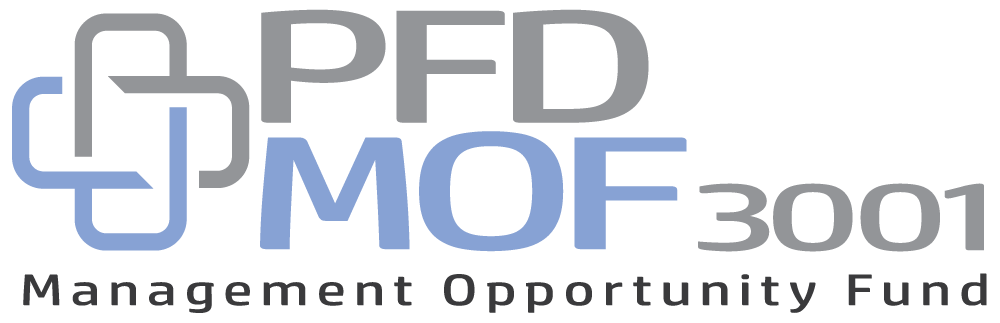
A medical account receivables and medical technology finance fund offering a fixed rate return with additional equity participation in targeted new medical technology opportunities.
SAFE HARBOR DECLARATION
THE STATEMENTS, PROJECTIONS AND ESTIMATES OF FUTURE PERFORMANCE OF THE COMPANY OR VARIOUS ELEMENTS OF THE COMPANY’S BUSINESS CONTAINED IN THIS MEMORANDUM THAT ARE NOT HISTORICAL FACTS ARE FORWARD-LOOKING STATEMENTS. INVESTORS SHOULD EXPECT THAT ANTICIPATED EVENTS AND CIRCUMSTANCES MAY NOT OCCUR, THAT UNANTICIPATED EVENTS AND CIRCUMSTANCES WILL OCCUR, AND THAT ACTUAL RESULTS WILL LIKELY VARY FROM THE FORWARD-LOOKING STATEMENTS. INVESTORS SHOULD BE AWARE THAT A NUMBER OF FACTORS COULD CAUSE THE FORWARD-LOOKING STATEMENTS OR PROJEC-TIONS CONTAINED IN THIS MEMORANDUM OR OTHERWISE MADE BY OR ON BEHALF OF THE COMPANY TO BE INCORRECT OR TO DIFFER MATERIALLY FROM ACTUAL RESULTS. SUCH FACTORS MAY INCLUDE, WITHOUT LIMITATION, (i) THE ABILITY OF THE COMPANY TO COMPLETE THE DEVELOPMENT OF ITS PRODUCTS IN A TIMELY MANNER, (ii) THE DEMAND FOR AND TIMING OF DEMAND FOR SUCH PRODUCTS, (iii) COMPETITION FROM OTHER PRODUCTS AND COMPANIES, (iv) THE RESULTS OF THE COMPANY’S SAFETY AND EFFICACY STUDIES, (v) THE RESULTS OF THE REGULATORY APPROVAL PROCESS, (vi) THE COMPANY’S SALES AND MAR-KETING CAPABILITIES, (vii) THE COMPANY’S ABILITY TO SELL ITS PRODUCTS PROFITABLY, (viii) THE ABILITY OF THE COMPANY’S THIRD-PARTY SUPPLIERS TO PROVIDE PRODUCTS AND SERVICES IN A RELIABLE MANNER; (ix) AVAILABILITY OF ADEQUATE DEBT AND EQUITY FINANCING, AND (x) GENERAL BUSINESS AND ECONOMIC CONDITIONS. THESE IMPORTANT FACTORS AND CERTAIN OTHER FACTORS THAT MIGHT AFFECT THE COMPA-NY’S FINANCIAL AND BUSINESS RESULTS ARE DISCUSSED IN THIS MEMORANDUM UNDER “RISK FACTORS.” THERE CAN BE NO ASSURANCE THAT THE COMPANY WILL BE ABLE TO ANTICIPATE, RESPOND TO OR ADAPT TO CHANGES IN ANY FACTORS AFFECTING THE COMPANY’S BUSINESS AND FINANCIAL RESULTS.